eco-DUOMIX
Instead of a mixing helix, the eco-DUOMIX is equipped with a mixing capsule optimized for dead space, which can be used for dynamic mixing for the first time. Materials with the same and/or different viscosities were developed and evaluated. The dead space optimized mixing capsule used, instead of a mixing spiral, is available as a consumable and is installed directly at the outlet of the dispenser. Inside the capsule, the motordriven mixer ensures optimum mixing, even of components that are difficult to process, despite the small volume. An exact application of even the smallest sealing beads is achieved by means of a replaceable metal dispensing needle, which is mechanically connected to the mixing capsule.
Product Description
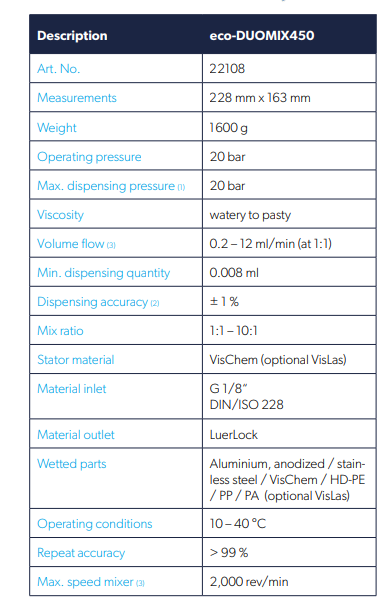
System presentation
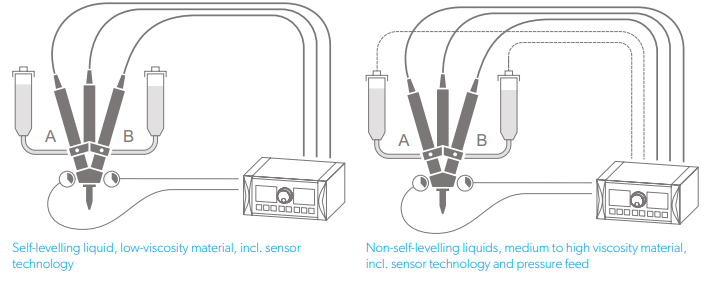
Comparison of mixing results at static and dynamic mixing with
the same volume flow and identical laboratory conditions:
The samples were run with the same control unit (calibration
and program were identical) and the same base pump (drives,
pump housing, rotor and stator, etc.). Only the way of mixing
the material was changed.
For the dosing tests, a difficult to process 2 component epoxy adhesive was used.
The mixing ratio is 10:1 (A:B) by weight.
The samples were prepared at different dosing speeds (0.5 ml/min – 6 ml/min).
As can be seen in Figure 1, the test material with the static mixing is not processable by default
– the material is only partially mixed and does not cure completely.
For the tests of the dynamic mixture, speeds of ~200 rpm, up to
~2000 rpm were used. As can be seen in Figure 2, this material
is already homogeneously mixed at the minimum speed, which
optically does not differ from the samples with higher dosing
speeds and mixer speeds.
Result: The 2-component epoxy adhesive, which could not be
processed by static mixing, is reliably mixed by dynamic mixing
even at the lowest mixer speed and can be processed optimally
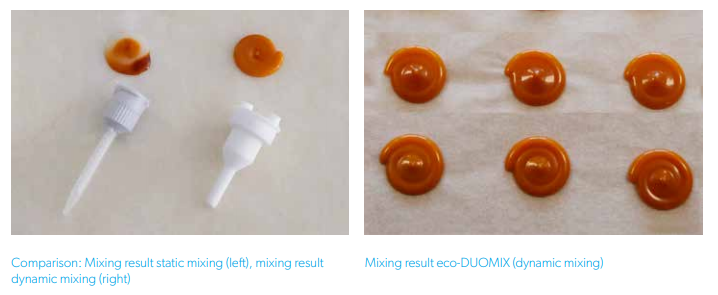